The event has a more or less rolling start - I got there (having ridden in on my bike from home) about 15 minutes are the first riders hit the course from just west of the (U.S.) Capitol, riding off through closed (to cars) streets in downtown DC, crossing the Roosevelt bridge into Virginia and heading north(ish) on the George Washington Parkway and heading a few miles down the Parkway before turning around and heading back up the Parkway, then the official route crossed back into DC for the finish (but I just road home).
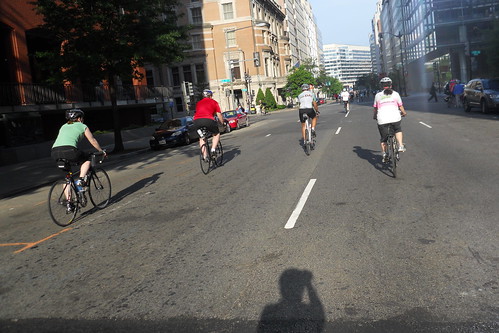
Sparse (relatively speaking) bike travel in downtown
Starting 20-25 minutes after the initial bunch seemed to work out well at this point - not too much (bike) traffic.

Not long before the Roosevelt Bridge, we rode through a short tunnel
After crossing the Roosevelt Bridge and approaching the GW Parkway, the bikes bunched up more.
Here you get a sense of the mix of riders - there are some spandex "we could go a lot faster types" but the crew on the tandem are just rolling along and then there are kids, too.
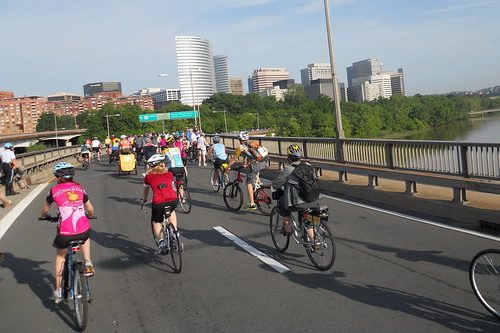
Nearing the GW Parkway
Beyond the Key Bridge the bike traffic became quite heavy - the bikes only had one side (two lines) of the divided highway, with bike traffic in each direction confined to one lane (with cones down the middle). Round about now I began to wish for more common sense and more common courtesy from my fellow riders. As we climbed, relatively slow moving (bicycle) traffic filled the entire single outbound lane. Some people riding uphill nonetheless impatiently tried "on the left" when what they meant was, "you're in my way; I want to go faster." Some crossed over into the oncoming lane (for bikes - usually a lane of traffic in the same direction) to pass the entire column, then pull in with the other riders (who would more or less have to let him or her in).
Some riders barreling down the GW Parkway on the return side presented a more intimidating picture - here there were some people whose cries of "on your LEFT" really sounded like "OUTTA MY WAY or I may run into you."
Now this sounds like chaos, but probably it was one in 250 or less that was acting in this way, but when you have thousands of riders on a few miles of road, 1-in-250 makes an impression.
Fortunately all the bike crashing I saw was small-time stuff and no one was significantly injured. I observed several obviously (or one assumes) really new riders fall for no particular reason and on the Parkway, fortunately while moving only a few miles per hour, a bike turned into another causing a tangle of metal and rubber.
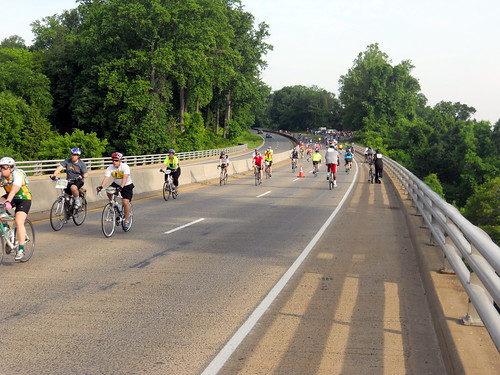
Nearing the turn around to head back on the GW Parkway
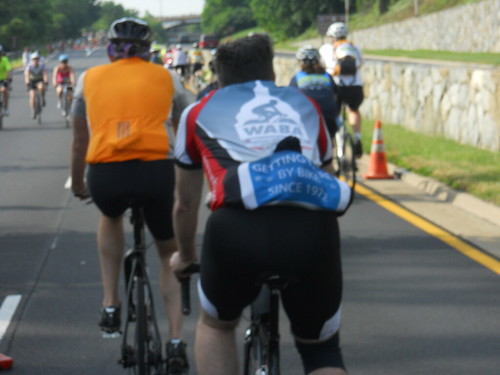
Last but not least - the one guy I saw who wasn't wearing a helmet, wearing a WABA jersey.
Yeah, image is a bit out of of focus, so his head looks funny - but there isn't a helmet on that head is what you can see readily enough. I don't believe wearing a helmet was required, but still.
The ride continued southbound on the GW Parkway and was, I thought, supposed to continue to the Air Force Monument, but at the Arlington Bridge there was some sort of accident (involving a cyclist? not clear at the time, or now for that matter) that had many emergency vehicles and a medevac helicopter. About a quarter mile beyond that was a turn around again on the GW Parkway to circle back and return into DC. Having had enough of a BikeDC experience for one day, I moved over to the GW bike trail and rode the eight or so miles home.
I guess overall I had an enjoyable experience, but I can't say I feel much of an urge to do it again at the moment, either.